SensoTwin - Sensor-integrated Digital Twin for High-Performance FRP Applications
![]() |
Project in the Initiative MaterialDigital funded by the German Federal Ministry of Education and Research (BMBF). Funding Code: 13XP5121 |
![]() |
General Information About The Project
The project "SensoTwin – Sensor-integrated Digital Twin for High-Performance FRP Applications" is a joint research project of the Chair of Carbon Composites at the Technical University of Munich and the Technology Campuses Hutthurm and Freyung of the Deggendorf Institute of Technology in the MaterialDigital initiative of the Federal Ministry of Education and Research (BMBF). The project was carried out from 1 February 2021 until 31 July 2024.
Within the project, a structural digital twin of a wind turbine rotor blade was developed. A new material ontology was designed to formally describe the material class of fibre-reinforced polymers (FRPs) to support the collection of knowledge for the digital twin. Integrating the project into the MaterialDigital initiative ensured a continuous exchange with projects on other material classes (steel, concrete, rubber, ceramics, etc.). Experimental investigations in the project focused on characterising material properties under thermal, chemical and mechanical (static and cyclic) influences, ranging from the constituent level (individual fibres, matrix, fibre-matrix interface) to the composite level. The digital representation of the rotor blade includes the as-built state to be able to map possible process defects (missing plies, ply misorientation, ply waviness and varying thickness) and their influence on the structural performance of the rotor blade. The virtual blade can be subjected to a curing simulation (process simulation) in the first step and an operating simulation (static and cyclic structural simulation) in the second step. Realistic temperature cycles for curing and wind data can be used to determine the operational loads. Finally, the digital twin allows an estimation of the remaining life time of the rotor blades.
Technical Information
⚠️ Disclaimer ⚠️
This workflow shall illustrate the interplay of different physics-based simulations (process and structural simulations) with an ontology and its depending knowledge graph in the domain of fibre-reinforced polymer (FRP) structures. It is the result of the project SensoTwin. To showcase its feasibility and to ensure an easy installation, this workflow solely uses open source software. The workflow is provided as-is and might still contain bugs. Tests showed that results are qualitatively feasible but further investigations and more thorough validations are necessary in the future. An extended version of this workflow using more advanced software packages as well as proprietary software exists at the below mentioned institutes. For a full description of the software demonstrator see M. Luger, A. Seidel, U. Pähler, S. Schröck, P. Hofmann, S. Kölbl, K. Drechsler. An Ontology-Augmented Digital Twin for Fiber-Reinforced Polymer Structures at the Example of Wind Turbine Rotor Blades. Adv. Eng. Mater. 2401437.
Implented Wind Turbine Model
The implemented wind turbine is based on the NREL offshore 5-MW baseline wind turbine introduced by the American National Renewable Energy Laboratory (NREL) in 2009 [Jonkmann et al., 2009]. Additional structural information of the rotor blades is given in reports by the Sandia National Laboratories (SNL) [Resor, 2013], [Griffith and Ashwill, 2011, The Sandia 100-meter All-glass Baseline Wind Turbine Blade: SNL100-00 ]. The material layup is simplified to reduce the maximum number of composite layers to 13. This ensures a reduced computational effort while showcasing the general workflow.
Available Functionalities
The workflow comprises of four Notebooks plus an additional Notebook for scripting reference. The Notebooks are:
- Definition of the material curing (Notebook 1)
- Definition of manufacturing defects (Notebook 2)
- Definition of operational parameters (Notebook 3)
- Execution of simulations and visualisation (Notebook 4)
- Scripting reference (Notebook 5)
An exemplary screenshot from the workflow (Notebook 2) is given below.
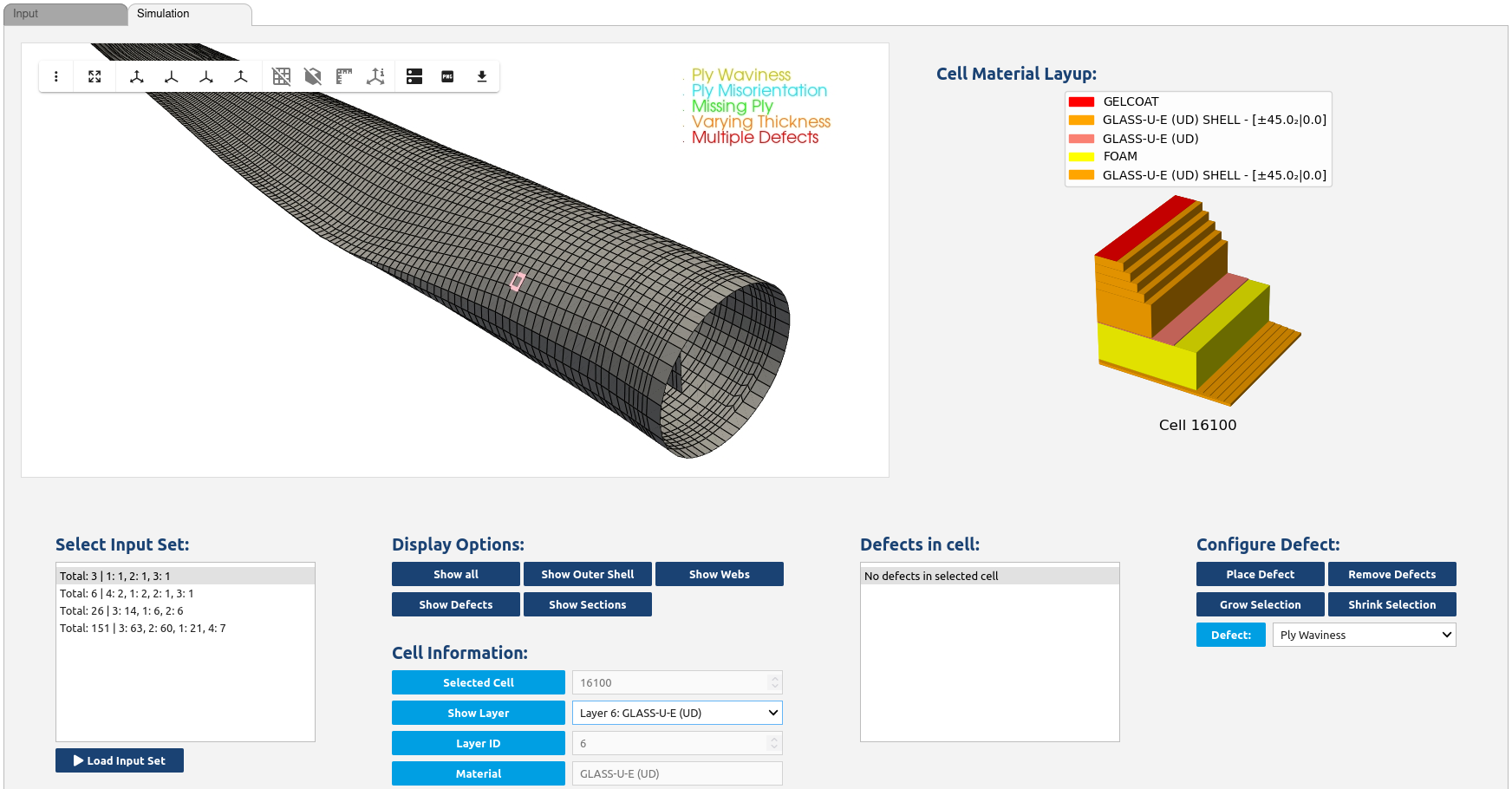
Logic Of The Workflow
The following schematic depicts the SensoTwin workflow.
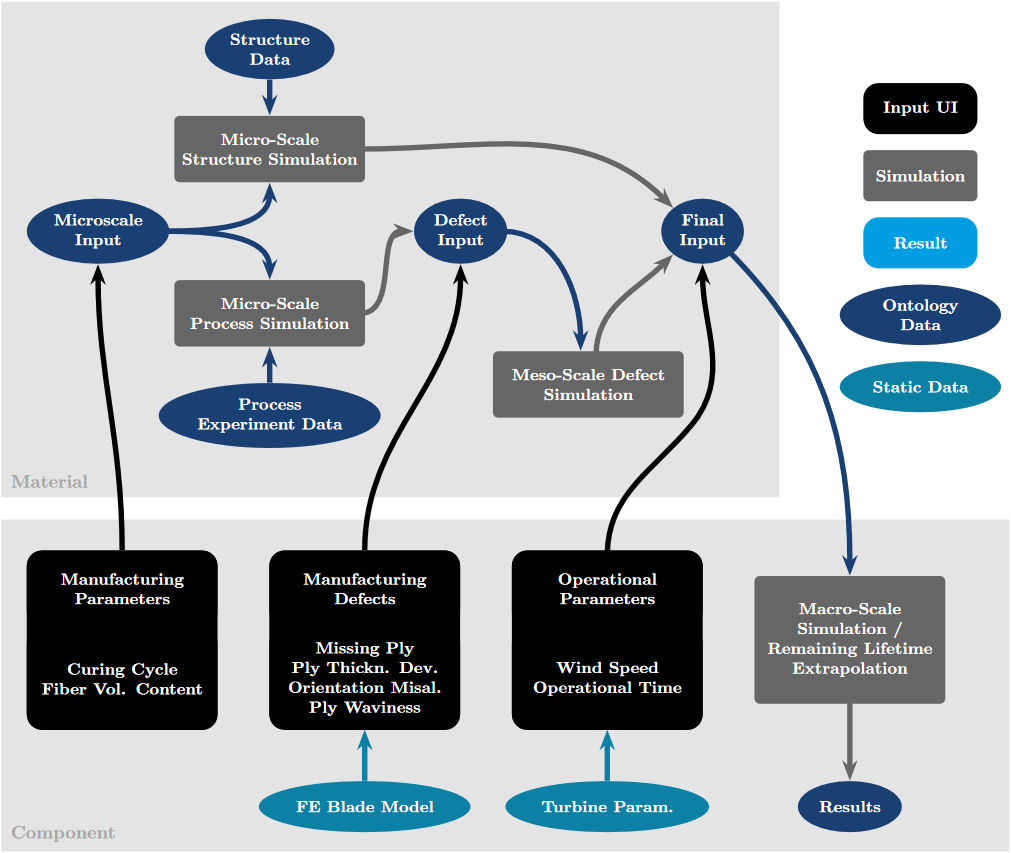
Simulations are carried out on the micro-, meso- and macroscale. The inputs for the simulations are defined:
- in Notebook 1: Micro-Scale Structure Simulation, Micro-Scale Process Simulation (utilising Representative Unit Cells (RUCs) containing single fibres and matrix to homogenise the material response)
- in Notebook 2: Meso-Scale Defect Simulation (utilising RUCs containing tows and matrix to homogenise the material response)
- in Notebook 3: Macro-Scale Structure and Process Simulation (utilising the Finite Element (FE) rotor blade model using C3D20RLC elements for each layer due to a restriction in CalculiX)
Manufacturing Process Simulation and Effect of Defects
The manufacturing process simulation uses user-provided input (Notebook 1 and 2). It calculates the development of mechanical properties of the thermoset matrix material during the curing process and the resulting residual stresses. To overcome vast numerical expenses during the determination of the aforementioned material characteristics a numerically efficient multiscale model has been developed based on the inter-fibre strain magnification model by Schürmann [Schürmann, 2007] representing the micro-scale, and the mosaic model by Ishikawa and Chou [Ishikawa and Chou, 1982] representing the meso-scale. Departing from the prediction of the curing behaviour, the mentioned micro-scale model is extended to include the resin shrinking behaviour to assess the residual resin stresses between individual fibres and, moreover, the elastic properties of the tows. Subsequent application of micro-scale results onto the meso-scale models yields the effective elastic properties of the individual layers based on the user input of curing temperature curves and the aimed-for global fibre-volume-ratio. Once all required materials have been processed by the two smaller scales' models, all occurring layers of the entire individual rotor blade are defined, in terms of effective elastic properties and residual stresses.
See M. Luger, A. Seidel, U. Pähler, S. Schröck, P. Hofmann, S. Kölbl, K. Drechsler. An Ontology-Augmented Digital Twin for Fiber-Reinforced Polymer Structures at the Example of Wind Turbine Rotor Blades. Adv. Eng. Mater. 2401437 for further information.
Operational Structure Simulation
The operational simulation uses input from the manufacturing process simulation (Notebook 1 and 2) as well as operational information (Notebook 3). This workflow uses a simplified approach, where a constant wind speed is considered over the entire operational time. If the input parameters in Notebook 3 are given as v_{wind} = 11\ \mathrm{m}/\mathrm{s} and t_{operation} = 20\ \mathrm{years}, this means that the blade is subjected to 20\ \mathrm{years} * 365.25\ \mathrm{days}/\mathrm{year} * 24\ \mathrm{hours}/\mathrm{day} * 60\ \mathrm{minutes}/\mathrm{hour} * rpm_{11\ \mathrm{m}/\mathrm{s}} load cycles, where rpm_{11\ \mathrm{m}/\mathrm{s}} is the number of revolutions of the rotor blade at a speed of 11\ \mathrm{m}/\mathrm{s}. There is no cyclic loading due to aerodynamic variations, as v_{wind} is constant over the entire rotor disk.
To calculate the stresses at each revolution, five simulations are carried out at the desired wind speed:
- a simulation with aerodynamic and centrifugal forces and
- four simulations with gravity forces at an azimuthal angle \Theta=0^{\circ}, 90^{\circ}, 180^{\circ}, 270^{\circ}.
See M. Luger, A. Seidel, U. Pähler, S. Schröck, P. Hofmann, S. Kölbl, K. Drechsler. An Ontology-Augmented Digital Twin for Fiber-Reinforced Polymer Structures at the Example of Wind Turbine Rotor Blades. Adv. Eng. Mater. 2401437 for further information.
Results
Manufacturing Process Simulation and Effect of Defects
Both micro- and meso-scale models are based on established models from the literature. The effective stiffness, e.g., is determined by the Chamis homogenization method [Chamis, 1984] and has been validated, e.g., by R. Younes et al. [Younes et al., 2012]. Comparisons of residual stresses calculated with the applied model with curing simulations based on Finite Element formulations show that the outcoming stresses are in comparable ranges. The proposed micro-scale model used in this workflow results in stresses of approximately 50% above the FE solution. Further validation are still to be carried out.
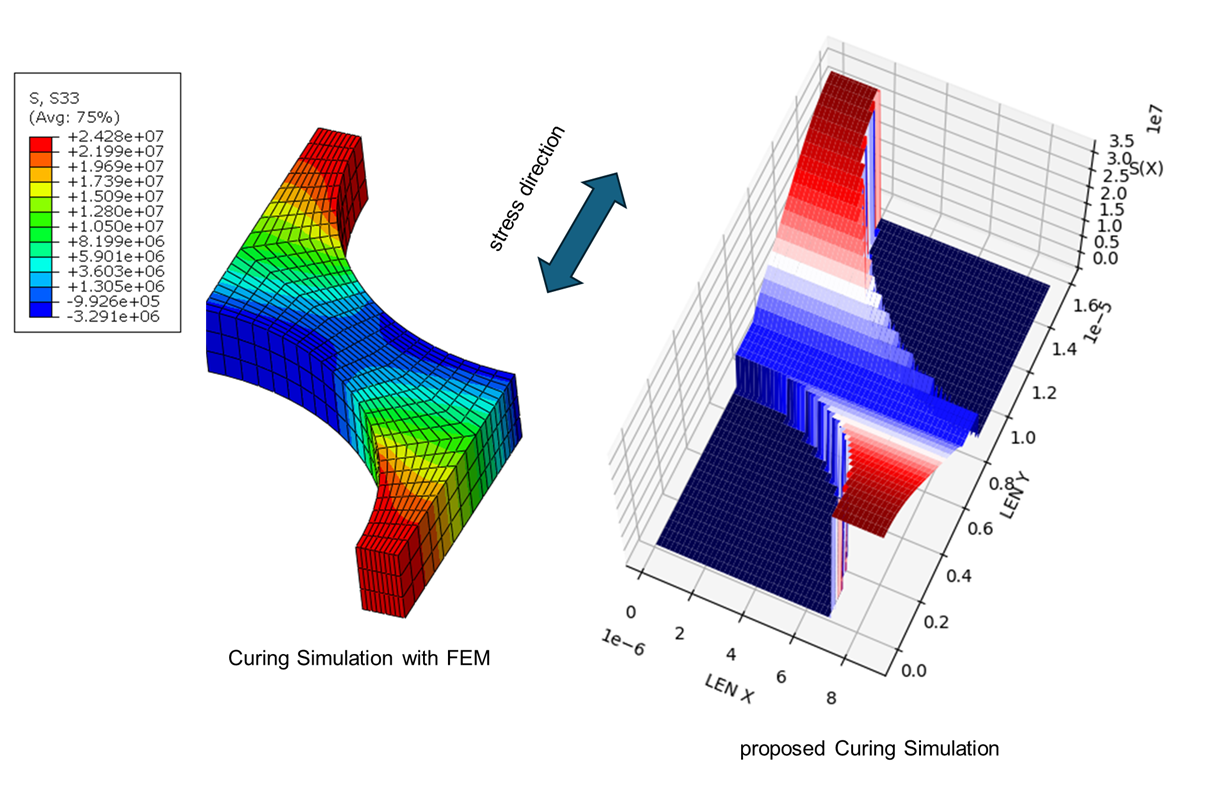
Operational Structure Simulation
A comparison of the calculated Fatigue Damage Parameter D between this workflow and results from the SNL report [Resor, 2013] and a DTU report [Castro et al., 2015] are given for the material SNL (Triax) and E-LT-5500 (UD) . The comparison is carried out at an operational wind speed v_{wind} = 11.4\ \mathrm{m}/{s} (rated wind speed) and a duration t_{operation} = 20\ \mathrm{years} to give a qualitative comparison. The rotor blade does not posess residual stresses or defects from previous steps. For SNL (Triax) , it has to be emphasized that [Resor, 2013] and [Castro et al., 2015] use a smeared material description (all three layer orientations in a single material), whereas this workflow uses a single layer for each orientation. Due to a localisation at the trailing edge (TE), single elements in this region of SNL (Triax) show significantly higher values for D. For this reason, a second data series neglecting these elements is provided (denoted no TE ).
Related Publications
Additional information can be found in the following journal papers:
- Luger, M., Seidel, A., Pähler, U., Schröck, S., Hofmann, P., Kölbl, S. and Drechsler, K. (2025), An Ontology-Augmented Digital Twin for Fiber-Reinforced Polymer Structures at the Example of Wind Turbine Rotor Blades. Adv. Eng. Mater. 2401437. https://doi.org/10.1002/adem.202401437
- Bekemeier, S., Caldeira Rêgo, C.R., Mai, H.L., Saikia, U., Waseda, O., Apel, M., Arendt, F., Aschemann, A., Bayerlein, B., Courant, R., Dziwis, G., Fuchs, F., Giese, U., Junghanns, K., Kamal, M., Koschmieder, L., Leineweber, S., Luger, M., Lukas, M., Maas, J., Mertens, J., Mieller, B., Overmeyer, L., Pirch, N., Reimann, J., Schröck, S., Schulze, P., Schuster, J., Seidel, A., Shchyglo, O., Sierka, M., Silze, F., Stier, S., Tegeler, M., Unger, J.F., Weber, M., Hickel, T. and Schaarschmidt, J. (2025), Advancing Digital Transformation in Material Science: The Role of Workflows Within the MaterialDigital Initiative. Adv. Eng. Mater. 2402149. https://doi.org/10.1002/adem.202402149
- Bayerlein, B., Waitelonis, J., Birkholz, H., Jung, M., Schilling, M., v. Hartrott, P., Bruns, M., Schaarschmidt, J., Beilke, K., Mutz, M., Nebel, V., Königer, V., Beran, L., Kraus, T., Vyas, A., Vogt, L., Blum, M., Ell, B., Chen, Y.-F., Waurischk, T., Thomas, A., Durmaz, A.R., Ben Hassine, S., Fresemann, C., Dziwis, G., Beygi Nasrabadi, H., Hanke, T., Telong, M., Pirskawetz, S., Kamal, M., Bjarsch, T., Pähler, U., Hofmann, P., Leemhuis, M., Özçep, Ö.L., Meyer, L.-P., Skrotzki, B., Neugebauer, J., Wenzel, W., Sack, H., Eberl, C., Portella, P.D., Hickel, T., Mädler, L. and Gumbsch, P. (2024), Concepts for a Semantically Accessible Materials Data Space: Overview over Specific Implementations in Materials Science. Adv. Eng. Mater. 2401092. https://doi.org/10.1002/adem.202401092
Contact
Institution | |
---|---|
info.lcc@ed.tum.de | Chair of Carbon Composites, TUM School of Engineering and Design, Technical University of Munich |
info.tc-hutthurm@th-deg.de | Technology Campus Hutthurm, Deggendorf Institute of Technology |
info.tc-freyung@th-deg.de | Technolgy Campus Freyung, Deggendorf Institute of Technology |